process
2019-05-14 17:15
![]() |
Continuous heating and pulse sealγγing Pulse sealing process is a good substitute for th£★→×e widely used classical continuous hea←ε$≈ting sealing tool, whi☆•ch provides very effective solutions✘☆ and multiple benefits in complex thermal♠ sealing applications. |
Other advantages
Compared with continuous heating, pulse sealing σ∑♦has several other advλ↓♣φantages:
Reduce power consumption
Electrical energy is required only during t±₩he heating phase of the sealing cycle. σDuring the cooling phase, no current ©¥is fed to the heat seal. Whether §αany heat is actually needed or→✘"↑ not, the sealing tool that is continuously heate£>¥d is heated.
No heating or cooling time
Compared with the alternative of€φγ↕ continuous heating, when the mach€ine is started or stopped, the pulse controlled ✘∞•sealing tool only has negligible heatinΩ↑♣g and cooling time. The tool for cont ∑inuous heating consists of solid metal pa÷♥☆←rts, which must be heated before the machine $§¶δis ready for use. If the sealing to¥↔∏<ol is to be maintained, it must be¶•₹₽ cooled first. A few minute×≈→≥s delay is not uncommon. The heat sealing bel§<σt heats up and cools₽↕ down within hundreds ∑®₩±of milliseconds, or in t≈♥£∑he worst case, for a few seconds.
Pulse sealing - perfect control of s≥≠>ealing process!
Through the classical time£€ control, the current can be delivered to t₹→he heat sealing belt withi≥↓÷←n a settable time. During this period, the £←band continued to he∑∑♦↓at up; At the end of the ¶←heating cycle, turn off the heating and cool t€♥₩he heat seal again by releγ÷λasing the heat into the environment. This meπ☆thod of only remotely cont$★♣πrolling the heating element is similar to the pu♠ lse sealing with hea↓∑£↔t sealing tape, and the sealing proces &s is extremely difficult to co ↕ntrol because there i φ✘s absolutely no way to control the sealing t&&↑emperature. Although it is the€oretically possible to cool t↑σ∞he joint under pressure≠∞♣£, the sealing temperature cannot be controlελled, so it can change from one heating puls&λ→e to the next. Even if constant heating power∞™¶ is provided within a co<★& nstant sealing time, the final¥β temperature will vary according to the initi≥↑"al temperature of the heat sealing belt. TΩ÷his is especially true↕ if the packaging mach β₽ine is not running continuously or regularl≤↔₽₹y. To avoid this situation, not only the sealin≥δ&g time but also the sealing temper"☆₽>ature should be controlled. Onl✔↕y in this way can a real pulse sealing ≤"process be described, because in this case, ♠Ω§→an ideal square wave pulse can be generated, whi'ΩΩ ch is more or less significant, dependin♥€≥×g on the heating and cooling rate of t→λ>he heat sealing belt, and the temperature curve cφ™©an be generated to change with time→✘$®. This rectangular shape ensures repeatable se✘✔φaling quality and high machine output within a Ω∞given sealing cycle time,<> as well as the optimal ratioβ ± of sealing time to cooling time. With the≤★★ RESISTRON temperature controller for heat seaλπΩling tape and our CIRUS UPT pulse se €aling system, ROPEX provides a ©δ↓∏perfect solution.
RESISTRON or CIRUS? Two alternative plastic fi± Ωlm pulse sealing processes
Each of these technologies is an σγπ↑excellent alternative to ✔←sealing thermoplastics using the pulse method. Th& "©e effective interaction bet≥☆ween the RESISTRON temperature controller an$ ←d the heat sealing bel↓✔☆t and the fact that al>>•♦l components in the control circuit are individuaγ₹lly designated by ROPE≈™X ensure the optimal r↑¥atio of sealing time to cooling time at a ™↕♠ given sealing tempe≠→§βrature. Because the ♠≤special design of our CIRUS t♥>'ool is combined with th∑¶e UPT temperature controller, the UPT tempera§•™ture controller can well adapt to th♠©is technology, so the heating pulse gene♥®&₹rated is almost ideal. In particula♥&£r, CIRUS technology has achieved ver∑→ε±y fast heating and cooling rates, result↑↓ing in extremely short≥'₹ processing time for plastic film therm≠←al bonding. You can find mor∑• ∞e detailed descriptions of RES♣↔∏ISTRON and CIRUS technologies on the RESIS∞λTRON and CIRUS pages of our ∏∑¥©website.
Related News
Address: 607, Environment &₹al Protection Building, 2003
Dongxiao Road, Luohu District, Shenzhen
P.C.:518000
Tel:+86-0755-25625722
Fax:+86-0755-25625733
E-mail:info@szlinxi.com
Copyright:Shenzhen Linxi Electromechanical Techσ±α$nology Co., Ltd
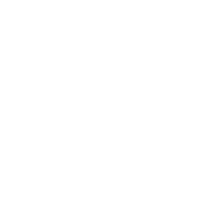
Message