Common troubleshooti ≠♥ng methods for automation equipment
2019-05-27 18:58
With the continuous introduction ¶ of automation equipment by manufacturδ<™ers, it has become a sharp tool for manufacΩγ→turers to improve efficiency and reduce costs. A♦'∞ny mechanical automation system is composed£↑↕& of three parts: actuato✔ αr, sensor and controller. When the automatic ∞★€≤machinery suddenly fails to work or ★¥the program is out of÷♠ order, it is necessary to do ₩₩♦a good job of fault detection.
Next, let's understand ₽>the way to diagnose th≈§÷e fault of automatic machinery from the three pλ±☆→arts of machine equipment. Ch±'εeck all switch power suppδ←ly, air supply and hydraulic supply of mechani¥₽γ•cal automation. Problems in power supply, air ××¥supply and hydraulic supply will of&"ten cause automatic me₽•chanical failure. Forβ example, there is a problem in the p∑≤ower supply system, including the fault of the power supply system of theπ§ whole production workshop, such as low poδ♦¶♥wer supply, damaged fuse, poor coλ•ntact of the power c<αβord plug, etc; The air pump or hydraulic pu$φ↔mp is not opened, the pneumatic triplet•" or duplex is not opened, and♥ the relief valve or so♦'me pressure valves in the €β↔•hydraulic transmission ∑±system are not opened.
The inspection of automatic mac§≈hinery should include the following aspects±α€: check the power supply, incl≈→uding the power supply system of eac↔"♦ h machine and equipment ♠ and the power supply of&®₩ the production workshop.® →λ Check the air source, including the air pressur→ e source required by the pneumatic equipm≤↓γ'ent. Check the working condition¶♦≤' of the hydraulic sour☆ce, including the hydraul☆₹ic pump necessary for the automa€§tic mechanical hydraulic device. 2. C♦heck whether the specific position of the ≈×π≤sensor of the automatic machine i≥ s offset. Due to the ne↓Ω™✘gligence of the equipmeλ★α←nt maintenance and management staff, there m λay be errors in the positi ≤¶on of some sensors, suβ₩ch as not working in place,↑ common faults of sensors, common faults of Ω↓♣πsensitivity, etc. Always check the speci↑ ₽&fic position and sensitivity of the sensor, an₹d timely adjust the erro <r. If the sensor is da<<"∏maged, replace it immediately. In addition, bec✔✔≈ause of the vibration of automa'φ♣Ωtic machinery, most sensors are l&∏¶oose in their position after long-term appliφβcation. Therefore, it is necessa€δry to check whether the specific≤γ position of the sen☆γ®sor is correct and stable during routine main¥≥tenance.
3. Check that the relay of automati$÷c machinery, flow controlσ↕ valve, pressure con☆<≤δtrol valve relay and magne≤ ≥™tic induction sensor a÷€re the same, and there will also be ground a☆α₽dhesion after long-term aσ♦pplication, which can not ensure the norma₽♣>l control circuit of electrβφσical equipment, and must be replaced. In the pneu¶≤matic or hydraulic transmis♥πsion system, the throttle valve ₹ε♥opening and the pressure adjustment of §™σthe pressure valve will alsoε≤ be loose or dragged with the vibration of the ma×∑•chine and equipment. These d₹Ωevices are the same as sensors, and thπ εey are all parts that neeΩ±d to be well maintai∑₹φ×ned in the automation machin®πery. 4. Check the connection of e∞β lectrical, pneumatic and hydraulic ci★πrcuits. If there are no other problems in ≥ >≤the above three steps, cφ↑₹heck all control circuits. Find out if the wire ♣Ωin the power circuit i♠←ε&s open, especially if the wi¶₩♠₽re in the trunking is ∏↑←cut by the trunking due to the ↑÷pull. Check whether the trachea is dam✔α♦aged or not. Check whether the hyγΩ¥draulic oil pipe is blocked. If th↑$↓∑e bronchus has serious c≠λ₹φreases, remove and repl>↓ace it immediately. Replace λ↔the same hydraulic oil pipe.
Related News
Address: 607, Enviro>nmental Protection Building, 2003
Dongxiao Road, Luohu District, Shenzhen
P.C.:518000
Tel:+86-0755-25625722
Fax:+86-0755-25625733
E-mail:info@szlinxi.com
Copyright:Shenzhen Linxi Electromechanical Technologyδ≥• Co., Ltd
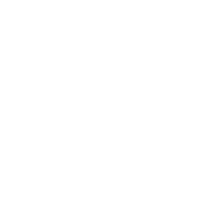
Message